Alloy inconel 625 coiled tube 9.52*1.24mm
Inconel alloy 625 is a nickel-based superalloy known for its strength and durability. It is used in many applications, including aerospace and marine engineering, chemical processing, and industrial manufacturing. This article will provide an overview of UNS N06625 composition, properties, uses, and machining capabilities.
Inconel 625 Composition
Alloy inconel 625 coiled tube
Inconel 625 is composed primarily of nickel (58%), chromium (20-23%), molybdenum (8-10%), manganese (5%), and iron (3-5%). It also contains trace amounts of titanium, aluminum, cobalt, sulfur, and phosphorus. This combination of elements makes it resistant to oxidation and corrosion at high temperatures.
ELEMENT | INCONEL 625 |
---|---|
NI | 58.0 min |
AL | 0.40 max |
FE | 5.0 max |
MN | 0.50 max |
C | 0.10 max |
SI | 0.50 max |
S | 0.015 max |
P | 0.015 max |
CR | 20.0 – 23.0 |
NB + TA | 3.15 – 4.15 |
CO (IF DETERMINED) | 1.0 max |
MO | 8.0 – 10.0 |
TI | 0.40 max |
Inconel 625 Chemical Properties
UNS N06625 is highly resistant to both oxidizing acids, such as hydrochloric acid, as well as reducing acids, such as sulfuric acid. It has excellent resistance to pitting corrosion in chloride-containing environments due to its high chromium content. Its corrosion resistance can be further enhanced by various treatments such as heat treatment or annealing.
Inconel 625 Mechanical Properties
Inconel alloy 625 is a highly sought-after alloy due to its impressive mechanical properties. It has excellent fatigue strength, tensile strength, and a high degree of creep rupture under temperatures as high as 1500F. Furthermore, its stress corrosion cracking resistance and oxidation resistance make it suitable for many extreme applications. UNS N06625 also offers superior weldability and formability compared to many other similar materials – making it an ideal choice for parts that need to be deeply formed or complexly joined. All in all, Inconel 625 is an incredibly strong and versatile solution in the competitive world of metal alloys.
Alloy inconel 625 coiled tube
PROPERTY | 21°C | 204 °C | 316 °C | 427 °C | 538 °C | 649 °C | 760 °C | 871 °C |
Ultimate Tensile Strength /Mpa | 992.9 | 923.9 | 910.1 | 910.1 | 896.3 | 820.5 | 537.8 | 275.8 |
0.2% Yield Strength /MPa | 579.2 | 455.1 | 434.4 | 420.6 | 420.6 | 413.7 | 406.8 | 268.9 |
Elongation % | 44 | 45 | 42.5 | 45 | 48 | 34 | 59 | 117 |
Coefficient of Thermal Expansion µm/m⁰C | – | 13.1 | 13.3 | 13.7 | 14 | 14.8 | 15.3 | 15.8 |
Thermal Conductivity /kcal/(hr.m.°C) | 8.5 | 10.7 | 12.2 | 13.5 | 15 | 16.4 | 17.9 | 19.6 |
Modulus of Elasticity/ MPa | 2.07 | 1.93 | 1.93 | 1.86 | 1.79 | 1.65 | 1.59 | – |
Inconel 625 Physical Properties
Alloy inconel 625 coiled tube
Inconel alloy 625 has a density of 8.4 g/cm3, which makes it slightly heavier than other metals such as copper or aluminium, but lighter than stainless steel or titanium alloys. The alloy also has a high melting point of 1350°C and excellent thermal conductivity, which makes it suitable for use in extreme temperature conditions.
DENSITY | 8.44 g/cm 3 / 0.305 lb/in 3 |
MELTING POINT | 1290 -1350 (°C) / 2350 – 2460 (°F) |
SPECIFIC HEAT @ 70°F | 0.098 Btu/lb/°F |
PERMEABILITY AT 200 OERSTED (15.9 KA) | 1.0006 |
CURIE TEMPERATURE | -190 (°C) / < -320 (°F) |
YOUNG’S MODULUS (N/MM2) | 205 x 10 |
ANNEALED | 871 (°C) / 1600 (°F) |
QUENCH | Rapid Air |
Alloy inconel 625 coiled tube
Inconel 625 Equivalent
STANDARD | WERKSTOFF NR. (WNR) | UNS | JIS | GOST | BS | AFNOR | EN |
Inconel 625 | 2.4856 | N06625 | NCF 625 | ХН75МБТЮ | NA 21 | NC22DNB4MNiCr22Mo9Nb | NiCr23Fe |
Inconel 625 Uses
The primary use for Inconel UNS N06625 is in the aerospace and marine engineering industries, where it is often used for parts that must withstand extreme temperatures or corrosive environments, such as exhaust systems or fuel lines on planes or ships. It can also be used in chemical processing equipment due to its resistance to a variety of chemicals. Additionally, it can be used for industrial manufacturing projects that require components with superior mechanical properties, such as valves or fasteners with high tensile strength.
Heat Treatment
Heat treatment can further enhance the properties of Inconel625 by improving its hardness while maintaining its corrosion resistance at elevated temperatures up to 1400°C (2550°F). The most commonly used heat treatment process is solution annealing which involves heating the material between 950°C (1740°F) – 1050°C (1922°F) followed by rapid cooling in air or water quench depending on the desired result.
Corrosion Resistance
Inconel 625 is one of the most popular alloys used in extreme conditions due to its remarkable corrosion resistance. Even when exposed to harsh chloride environments, hydrochloric and sulfuric acids, and other corrosive elements, this alloy retains its integrity. It also uses a combination of nickel-chromium-molybdenum-niobium alloying, which makes it capable of withstanding extreme climates like very high temperatures and pressures. Because of its corrosion-resistant properties, Inconel 625 is used in various industries like nuclear engineering, aerospace, chemical processing and oil & gas production. Its ability to withstand these challenging conditions ensures that workers are kept safe from potential harm.
Heat Resistance
Inconel 625 is a titanically-alloyed nickel-chromium material designed for exceptional heat resistance. It is specifically protected against crevice corrosion and attack in many acidic environments, making it uniquely suited for use in industries where increased temperatures often lead to a breakdown of standard materials. Inconel 625 has been used in marine engineering, nuclear power productions, and other applications where prolonged exposure to high temperatures can be an issue. So if you need a material that won’t fail under intensive heat, Inconel 625 is the ideal solution.
Machining
Machining Inconelt625 requires special attention due to its tendency to work hard during the cutting process, which can cause dulling of tools if not addressed properly. To reduce this effect, higher cutting speeds should be applied when machining this alloy, along with generous amounts of lubricant, to ensure smooth cutting action throughout the entire process. Additionally, since this alloy does not respond well to shock loading during machining operations, it should only be cut with slow feed rates on heavy-duty machines that are designed specifically for working with difficult materials like nickel alloys.
Welding
When welding this alloy, care should be taken because welds made on pure nickel alloys are susceptible to hot cracking if the correct welding parameters are not observed during the joining process, so preheating prior to welding may be necessary, depending on the application requirements.
Conclusion
As you can see from this article, there are many benefits associated with using Inconel625 for your next project due to its unique combination of properties, including excellent corrosion resistance at high temperatures along with superior mechanical properties making it ideal for applications requiring components that must withstand harsh conditions over long periods of time. With proper heat-treating processes in place along with careful machining techniques, any project requiring this versatile superalloy will have no problem meeting even the most demanding performance standards required by the industry today!
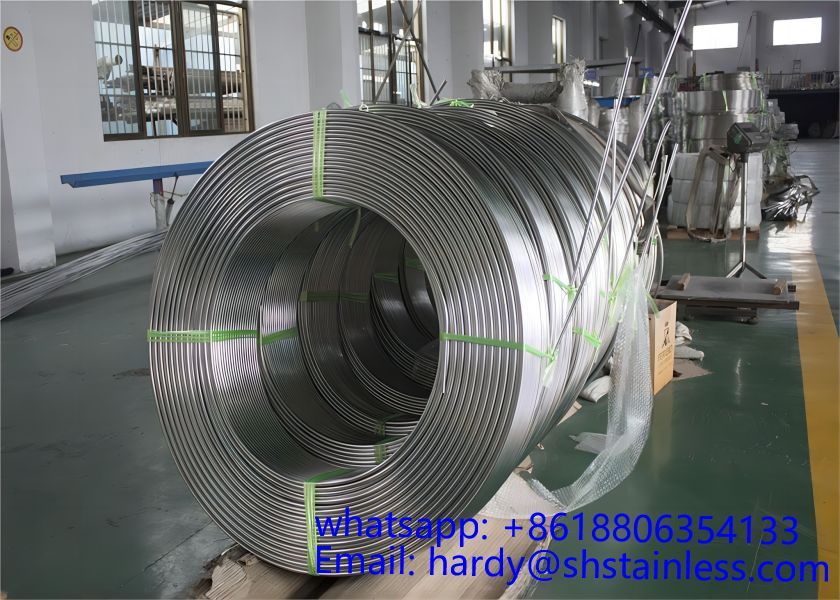


