Alloy 600 Stainless Steel Coil Tubing Price
Chemical Composition, %
Typical corrosion applications include titanium dioxide production (chloride route), perchlorethylene syntheses, vinyl chloride monomer (VCM), and magnesium chloride. Alloy 600 is used in chemical and food manufacturing and storage, heat treating, phenol condensers, soap manufacture, vegetable and fatty acid vessels and many more.
Ni + Co | Cr | Fe | C | Mn | S | Si | Cu |
72.0 min | 14.0-17.0 | 6.0-10.0 | .15 max | 1.00 max | .015 max | .50 max | .50 max |
In what applications is Inconel 600 used?
- Chemical industry
- Aerospace
- Heat treating industry
- Pulp and paper industry
- Food processing
- Nuclear Engineering
- Gas turbine components
ASTM Specifications
Pipe Smls | Pipe Welded | Tube Smls | Tube Welded | Sheet/Plate | Bar | Forging | Fitting | Wire |
B167 | B517 | B163 | B516 | B168 | B166 | B564 | B366 |
Mechanical Properties
Typical room temperature Tensile Properties of Annealed Material
Product Form | Condition | Tensile (ksi) | .2% Yield (ksi) | Elongation (%) | Hardness (HRB) |
Rod & Bar | Cold-Drawn | 80-100 | 25-50 | 35-55 | 65-85 |
Rod & Bar | Hot-Finished | 80-100 | 30-50 | 35-55 | 65-85 |
Tube & Pipe | Hot-Finished | 75-100 | 25-50 | 35*55 | - |
Tube & Pipe | Cold-Drawn | 80-100 | 25-50 | 35-55 | 88 Max |
Plate | Hot-Rolled | 80-105 | 30-50 | 35-55 | 65-85 |
Sheet | Cold-Drawn | 80-100 | 30-45 | 35-55 | 88 Max |
Inconel 600 Melting Point
Element | Density | Melting Point | Tensile Strength | Yield Strength (0.2%Offset) | Elongation |
Alloy 600 | 8.47 g/cm3 | 1413 °C (2580 °F) | Psi – 95,000 , MPa – 655 | Psi – 45,000 , MPa – 310 | 40 % |
Inconel 600 Equivalent
STANDARD | WERKSTOFF NR. | UNS | JIS | BS | GOST | AFNOR | EN |
Alloy 600 | 2.4816 | N06600 | NCF 600 | NA 13 | МНЖМц 28-2,5-1,5 | NC15FE11M | NiCr15Fe |
Alloy 600 Tubing
Alloy 600 is an excellent candidate for many uses in extremely high temperature and highly corrosive environments. The blend of nickel and chromium yields a solid resistance to oxidation in operating temperatures. These temperatures can range from cryogenic to scorching levels of 2,000°F. The high nickel content of alloy 400 also offers a nearly-complete resistance to stress corrosion cracking, which is commonly found in chloride environments.
It is important to note that the chromium portion of the alloy’s chemical profile makes it possible for the grade to withstand high temperatures. The finer grain structure of the cold finished tube, additionally, brings better corrosion resistance, which includes higher fatigue and impact strength values.
Product Specifications
ASTM B163, B167 / ASME SB163 / NACE MR0175, MR0103
Size Range
Outside Diameter (OD) | Wall Thickness |
.250”–.750” | .035”–.083” |
Chemical Requirements
Alloy 600 (UNS N06600)
Composition %
Ni Nickel |
Cu Copper |
Fe Iron |
Mn Manganese |
C Carbon |
Si Silicon |
S Sulfur |
Cr Chromium |
72.0 min | 0.50 max | 6.00–10.00 | 1.00 max | 0.15 max | 0.50 max | 0.015 max | 14.0–17.0 |
Dimensional Tolerances
OD | OD Tolerance | Wall Tolerance |
≤ .500” excl | +.005” | ± 12.5% |
.500”–.750” excl | +.005” | ± 12.5% |
Mechanical Properties
Yield Strength: | 35 ksi min |
Tensile Strength: | 80 ksi min |
Elongation (min 2"): | 30% |
Fabrication
Alloy 600 can be easily welded by standard process. The manageability of this alloy is excellent, residing between the utility of T303 and T304.
Factoy Photos
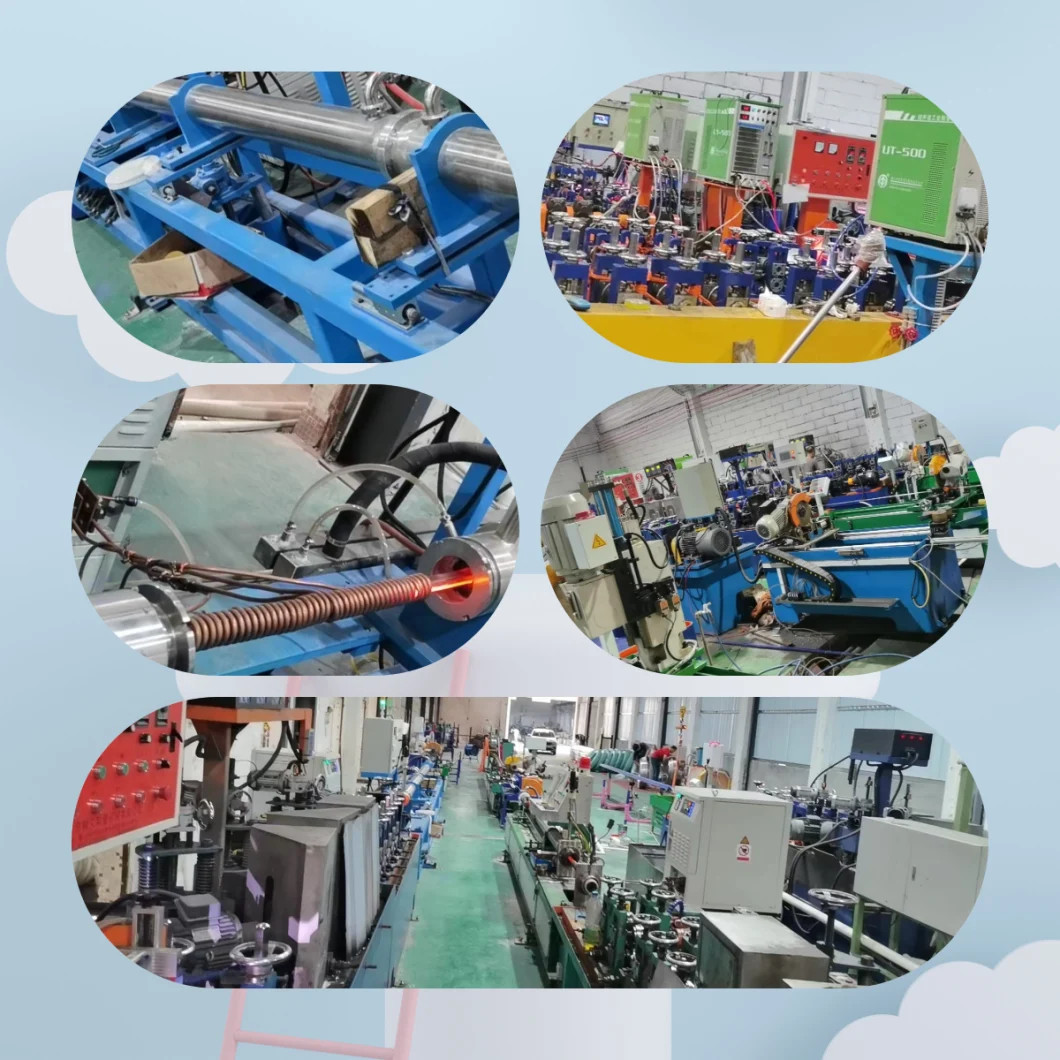
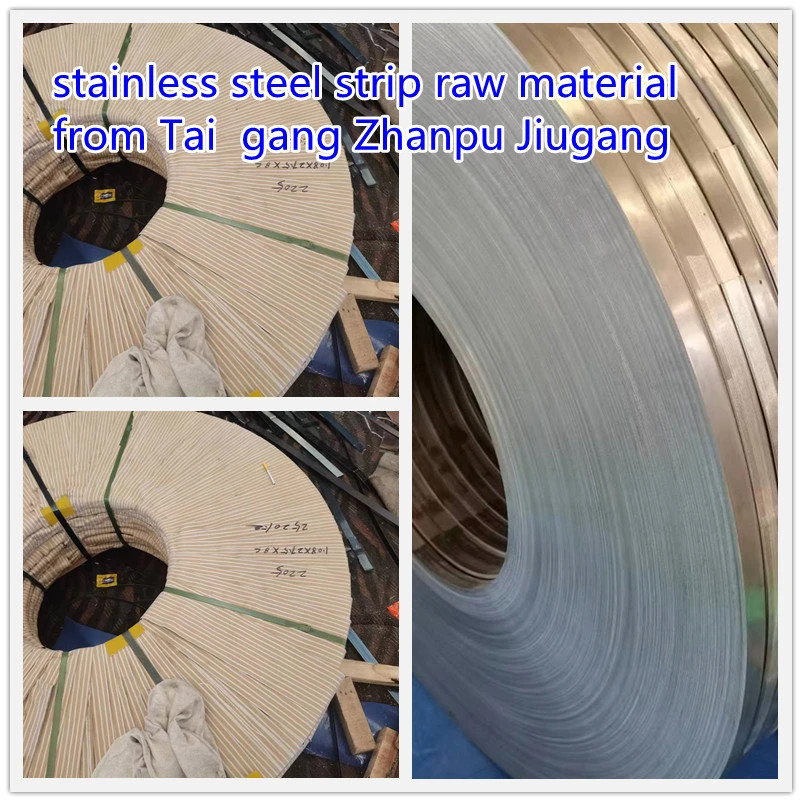
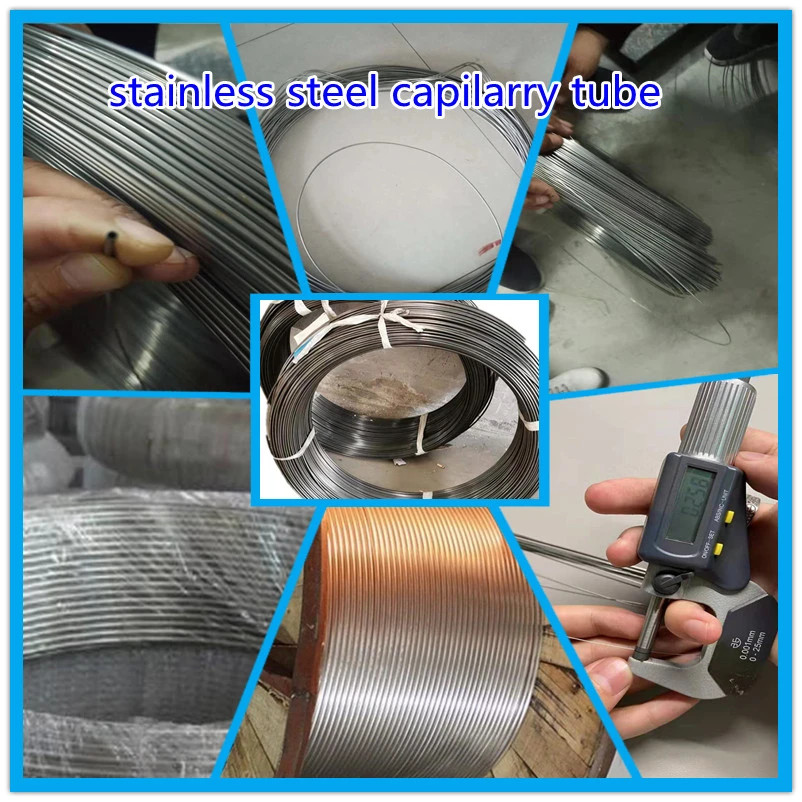
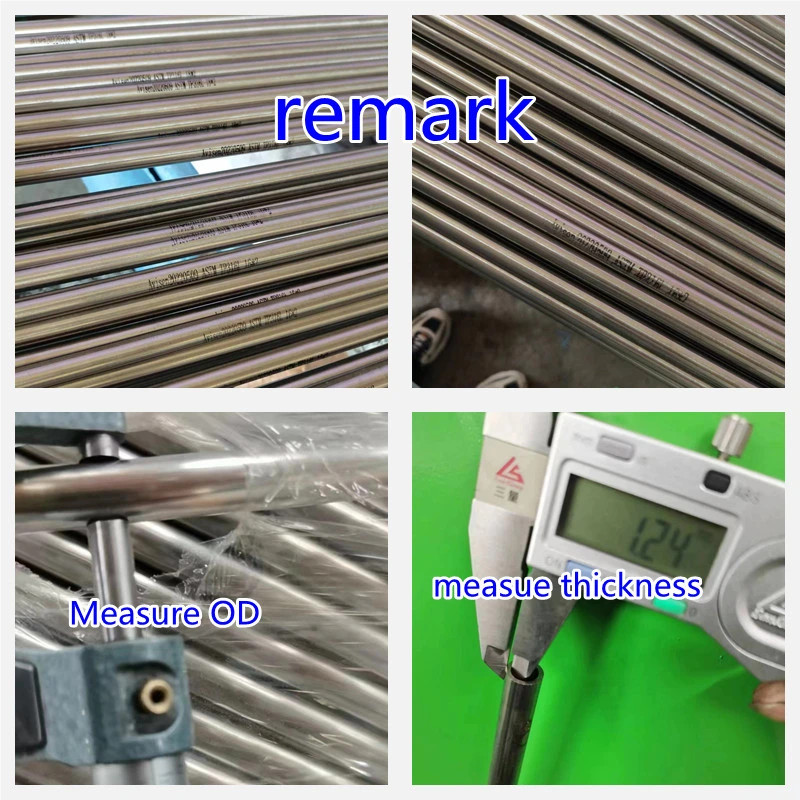
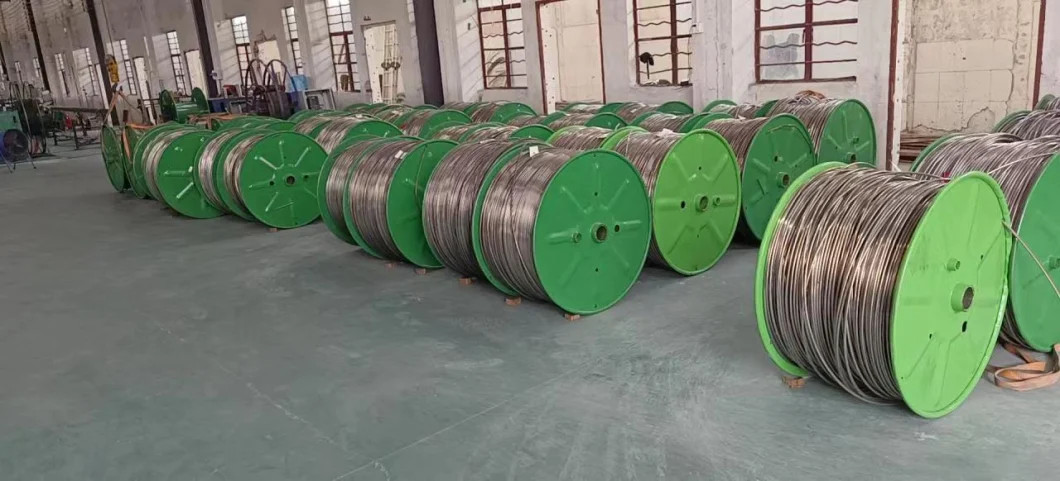
Inspection
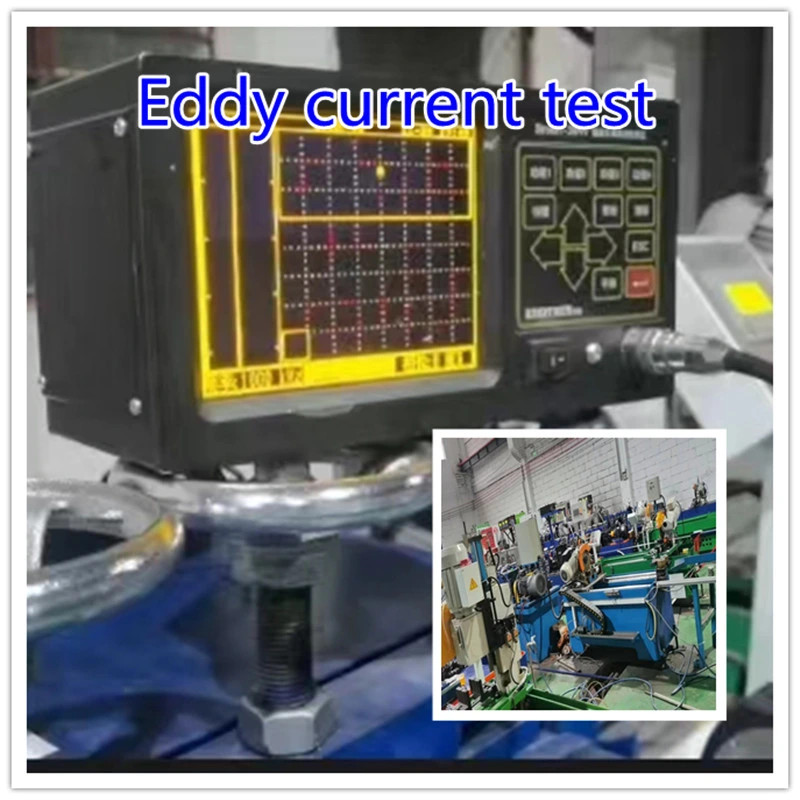
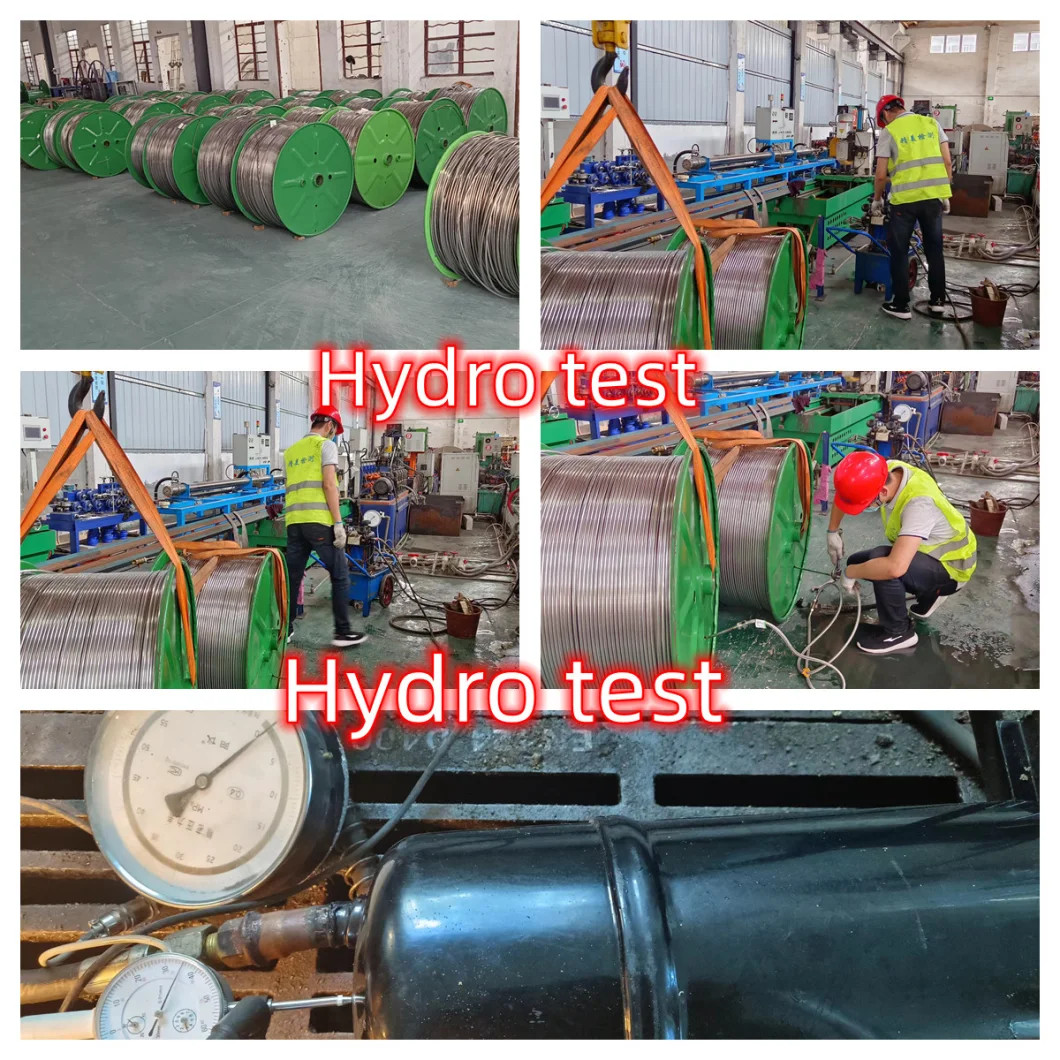
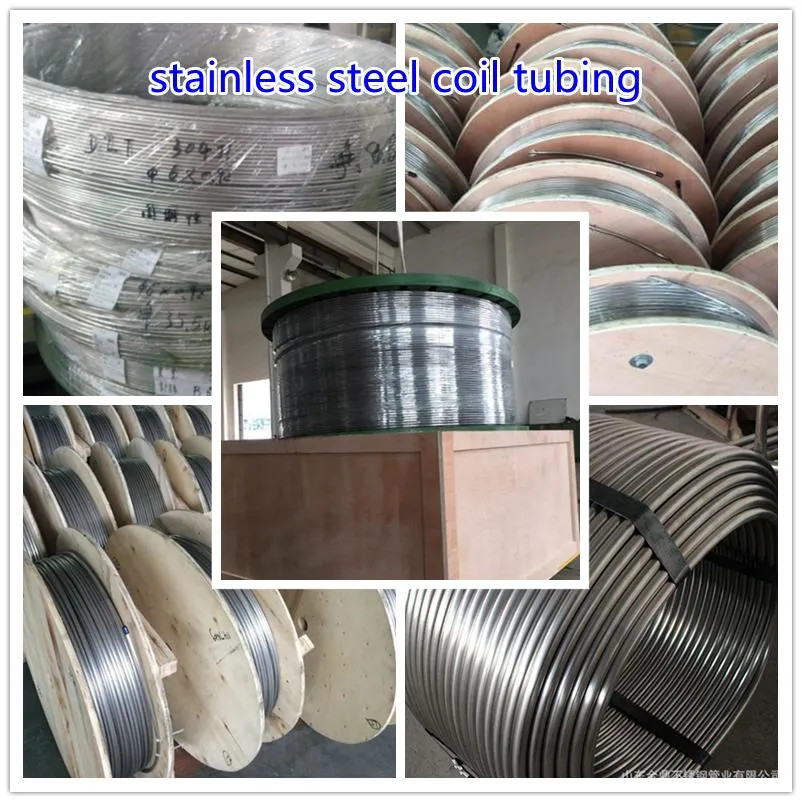
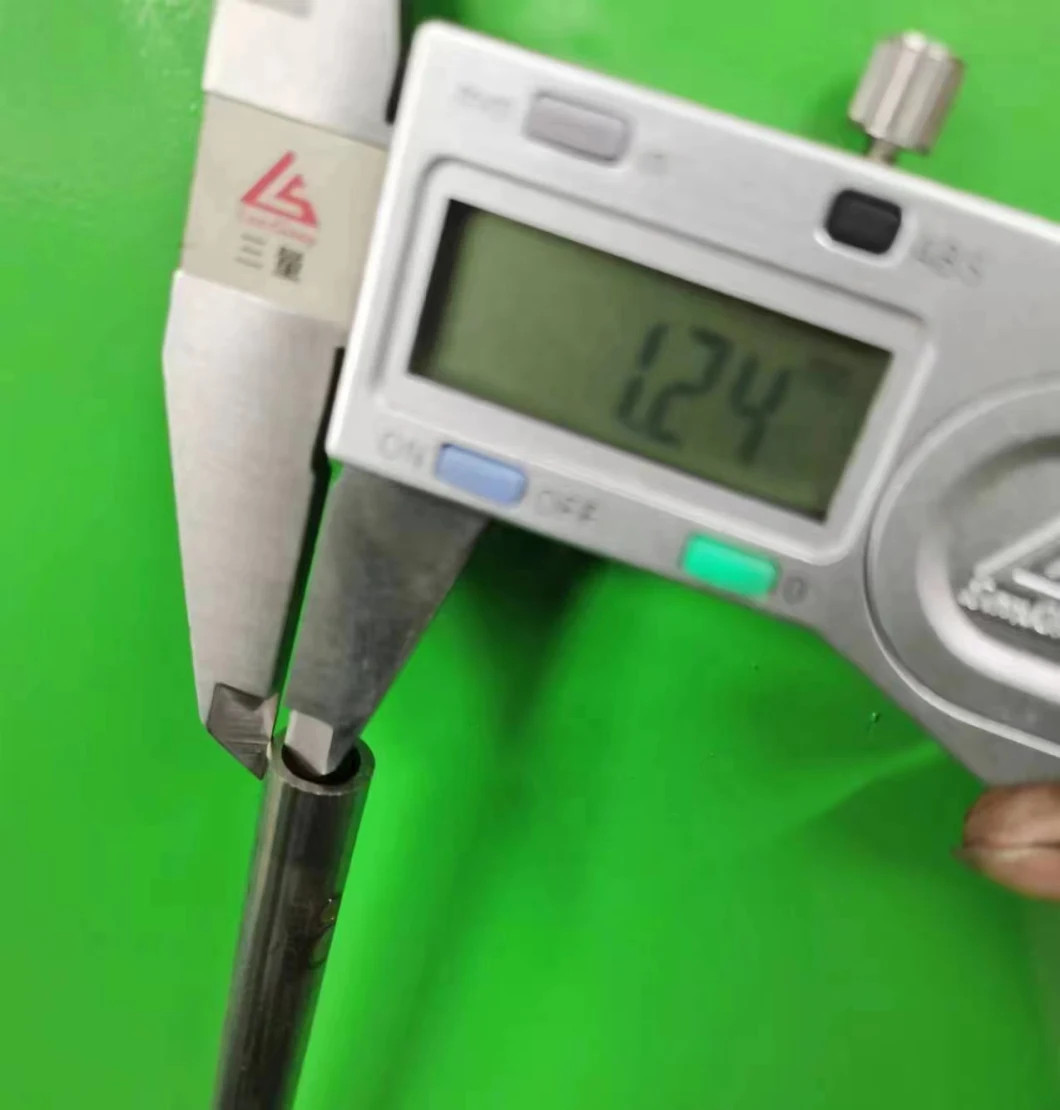
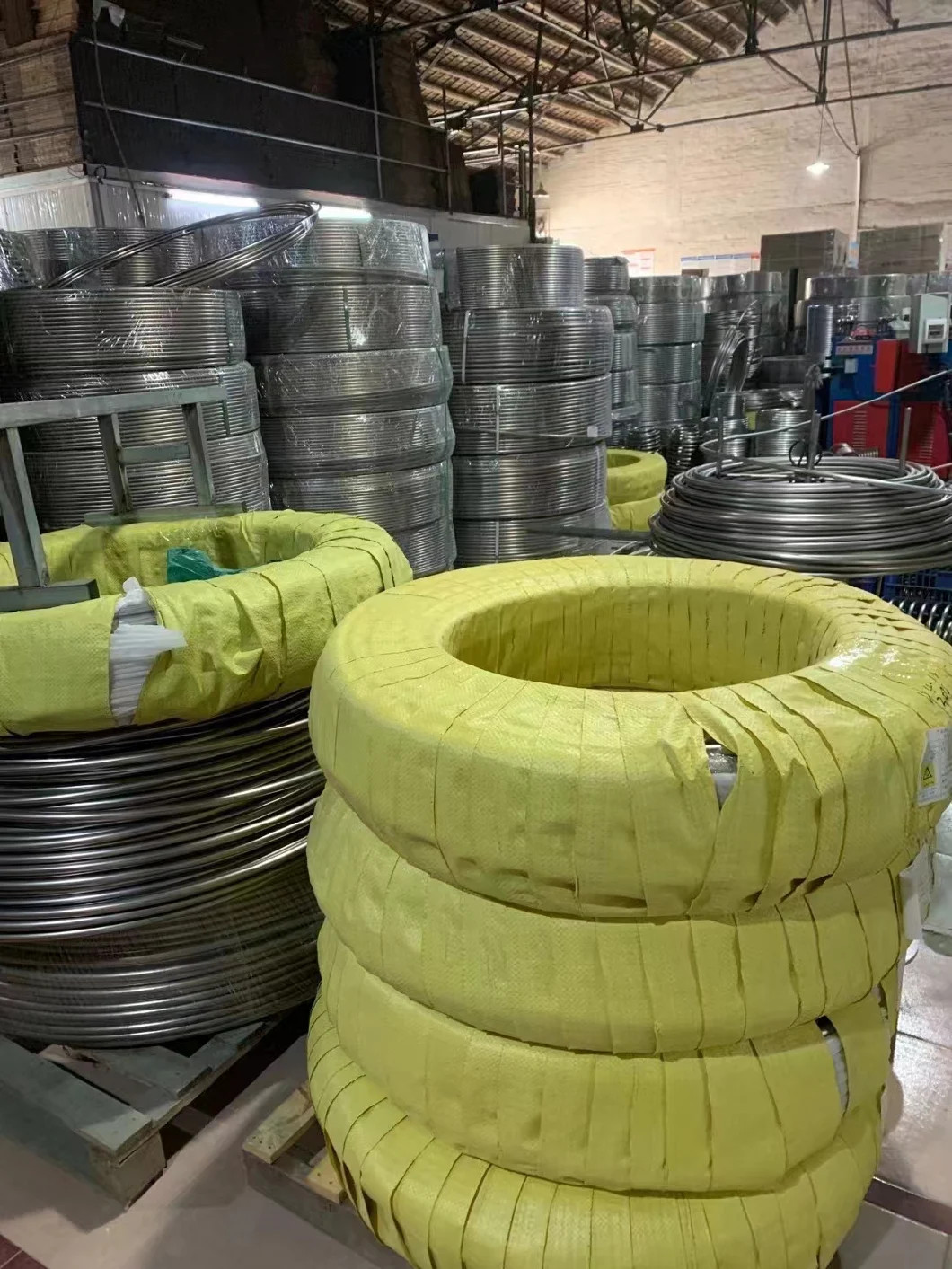
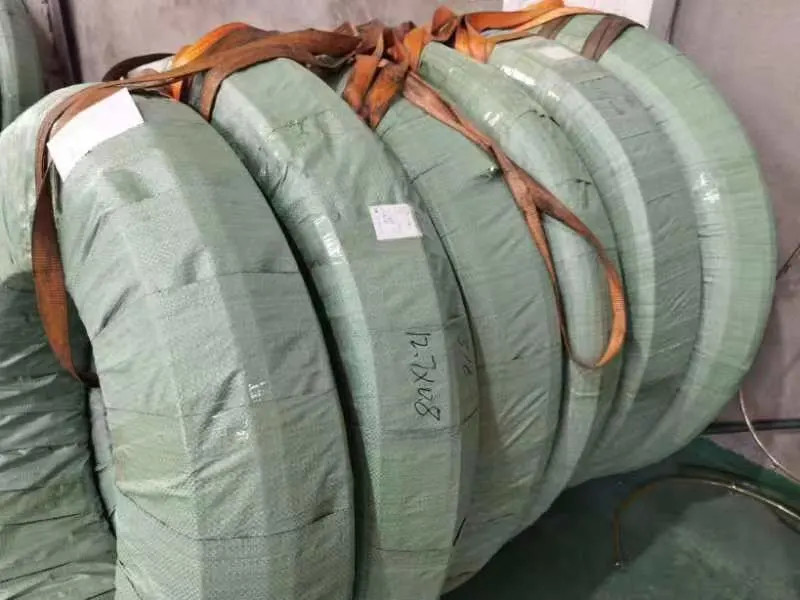
Shipping & Packing
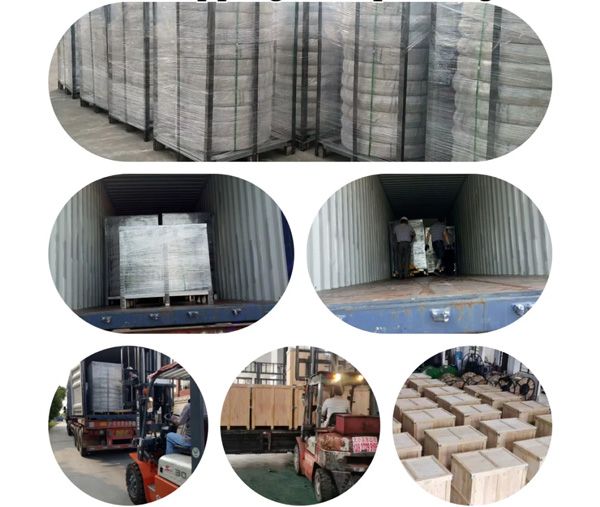
Test Report

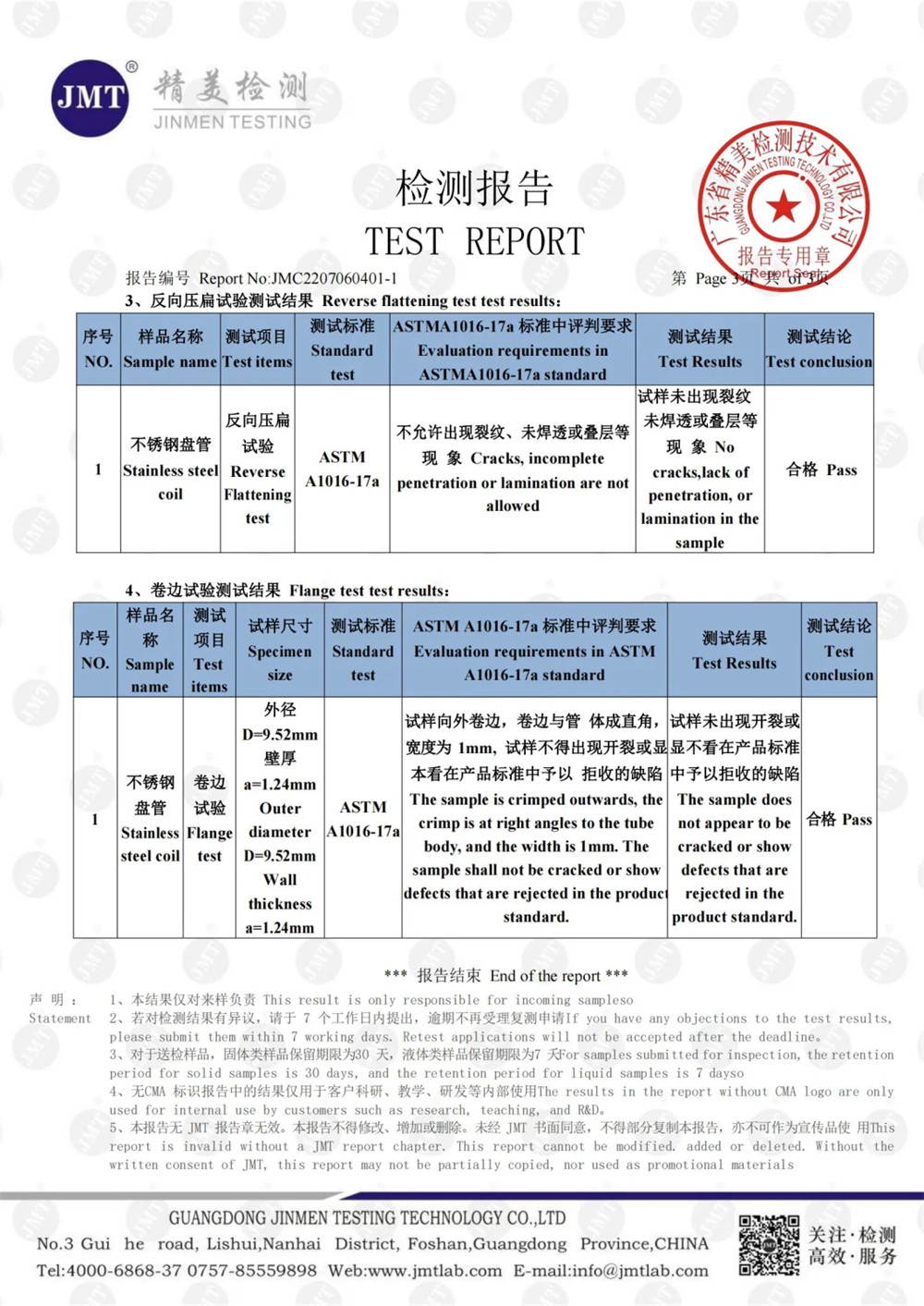
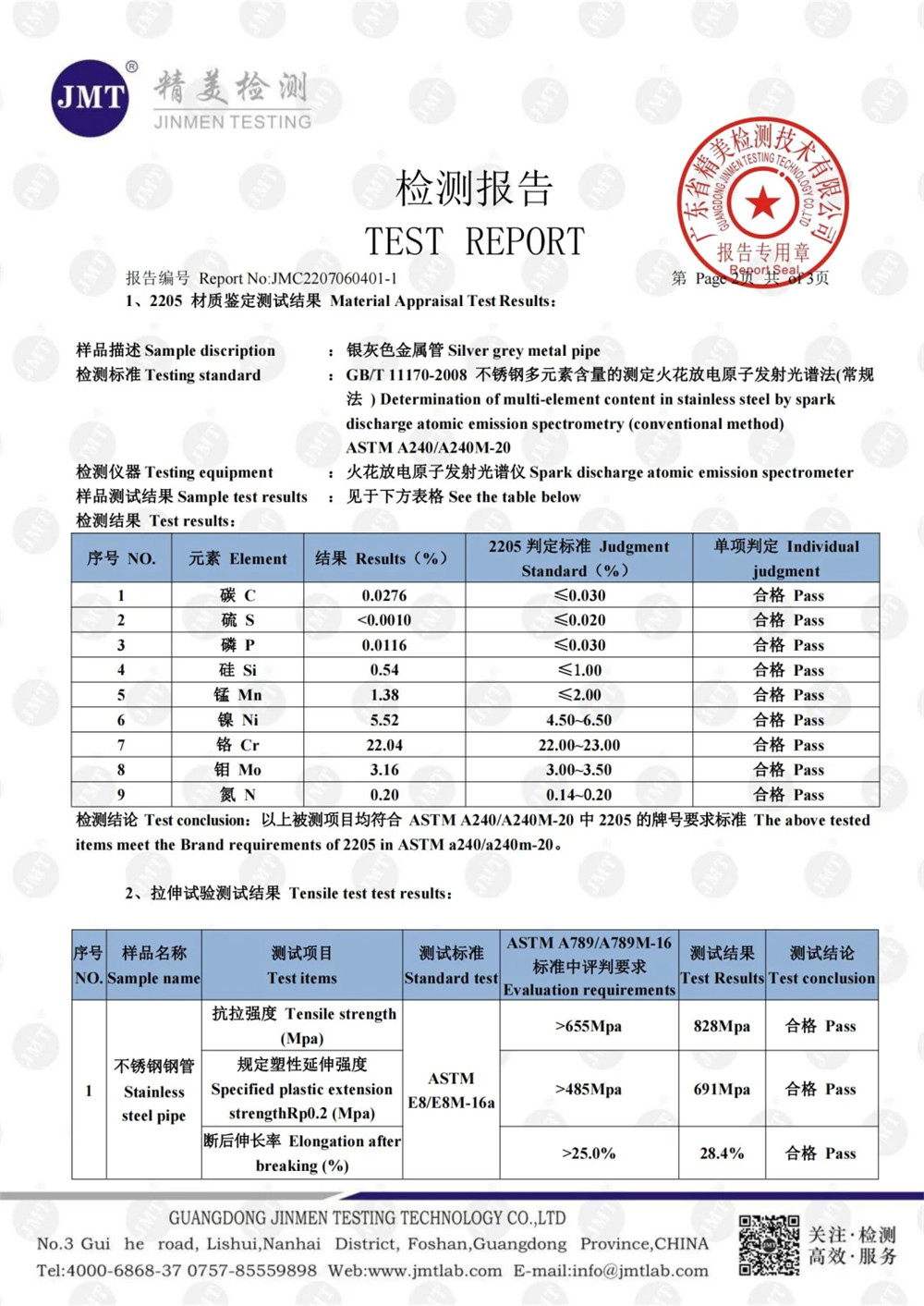