321 stainless steel 4.0*0.35 mm coiled tube
321 is a titanium stabilised chromium-nickel austenitic stainless steel with good strength and excellent corrosion resistance, as supplied in the annealed condition with a typical brinell hardness of 175.Characterised by high corrosion resistance in general atmospheric corrosive environments it exhibits excellent resistance to most oxidizing agents, general foodstuffs, sterilizing solutions, dyestuffs, most organic chemicals plus a wide variety of inorganic chemicals, also hot petroleum gases, steam combustion gases, nitric acid, and to a lesser extent sulphuric acid. It displays good oxidation resistance at elevated temperatures has excellent resistance to intergranular corrosion and has excellent weldability. 321 cannot be hardened by thermal treatment, but strength and hardness can be increased substantially by cold working, with subsequent reduction in ductility.
Used extensively for applications where the addition of titanium and its stabilizing effect as a carbide forming element allows it to be welded and/or used within the carbide precipitation range 430oC – 870oC without the risk of intergranular corrosion. These include Food Processing, Dairy Equipment, Chemical, Petrochemical, Transport and associated industries etc.
Material non magnetic in the annealed condition, but can become mildly magnetic following heavy cold working.
Annealing is required to rectify if necessary.
N.B. Optimum corrosion resistance is achieved in the annealed condition.
Australia | AS 2837-1986-321 |
Germany | W.Nr 1.4541 X6CrNiTi18 10 |
Great Britain | BS970 Part 3 1991 321S31 BS970 – 1955 EN58B/EN58C |
Japan | JIS G4303 SuS 321 |
USA | ASTM A276-98b 321 SAE 30321 AISI 321 UNS S32100 |
Chemical Composition | |||||||||||
Min. % | Max % | ||||||||||
Carbon | 0 | 0.08 | |||||||||
Silicon | 0 | 1.00 | |||||||||
Manganese | 0 | 2.00 | |||||||||
Nickel | 9.00 | 12.00 | |||||||||
Chromium | 17.00 | 19.00 | |||||||||
Titanium | 5 x Carbon | 0.80 | |||||||||
Phosphorous | 0 | 0.045 | |||||||||
Sulphur | 0 | 0.03 | |||||||||
Mechanical Property Requirements – Annealed to ASTM A276-98b 321 | |||||||||||
Finish | Hot Finish | Cold Finish | |||||||||
Dia or Thickness mm | All | Up to 12.7 | Over 12.7 | ||||||||
Temsile Strength Mpa Min. | 515 | 620 | 515 | ||||||||
Yield Strength Mpa Min. | 205 | 310 | 205 | ||||||||
Elongation in 50mm % Min. | 40 | 30 | 30 | ||||||||
Typical Mechanical Properties At Room Temperature – Annealed | |||||||||||
Finish | Cold Drawn | Other | |||||||||
Tensile Strength Mpa | 680 | 600 | |||||||||
Yield Strength Mpa | 500 | 280 | |||||||||
Elongation in 50mm % | 40 | 55 | |||||||||
Impact Charpy V J | 180 | ||||||||||
Hardness | HB | 200 | 165 | ||||||||
Rc | 15 | ||||||||||
Elevated Temperature Properties | |||||||||||
321 displays good oxidation resistance in continuous service up to 930oC, and in intermittent service up to 870oC.It can also be used within the carbide precipitation range 430oC – 870oC without the risk of intergranular corrosion. Mechanical properties are reduced as temperature increases.
|
|||||||||||
Typical Mechanical Properties – Annealed at Elevated Temperatures | |||||||||||
Temperature oC | 20 | 430 | 550 | 650 | 760 | 870 | |||||
Short – Time Tensile Tests | Tensile Strength Mpa | 580 | 425 | 365 | 310 | 205 | 140 | ||||
Yield Strength Mpa | 240 | 170 | 150 | 135 | 105 | 70 | |||||
Elongation in 50mm % | 60 | 38 | 35 | 32 | 33 | 40 | |||||
Creep Tests | Stress for 1% Creep in 10,000 Hours Mpa |
115 | 50 | 14 | |||||||
Low Temperature Properties | |||||||||||
321 has excellent low temperature properties with increased tensile and yield strengths with little loss of toughness in the annealed condition. | |||||||||||
Typical Mechanical Properties – Annealed at Zero and Sub-Zero Temperatures | |||||||||||
Temperature oC | 0 | -70 | -130 | -180 | -240 | ||||||
Tensile Strengt Mpa | 740 | 900 | 1135 | 1350 | 1600 | ||||||
Yield Strength Mpa | 300 | 340 | 370 | 400 | 450 | ||||||
Elongation in 50mm % | 57 | 55 | 50 | 45 | 35 | ||||||
Impact Charpy J | 190 | 190 | 186 | 186 | 150 |
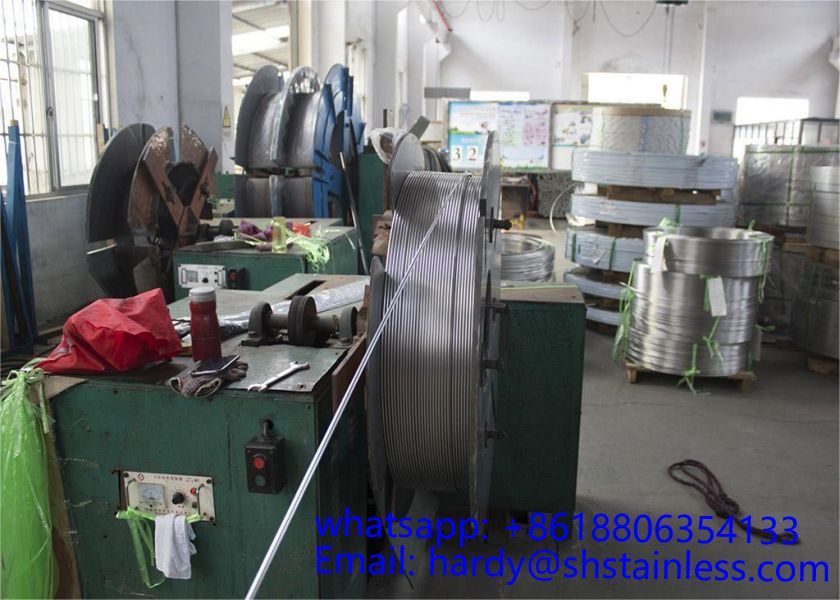


